Aluminium: a precious material
«Employ another metal instead of molten iron».
«Copper?» said Morgan
«No, that would be too heavy! ».
«What then?» asked the mayor.
«Aluminium!» replied Barbicane.
«Aluminium?» cried his three colleagues in chorus
Jules Vernes chose aluminium to build the spacecraft for the journey to the moon. In his book “From the Earth to the Moon”, written in 1865, lightness and resistance were the reasons of choice for this silver-white coloured metal.
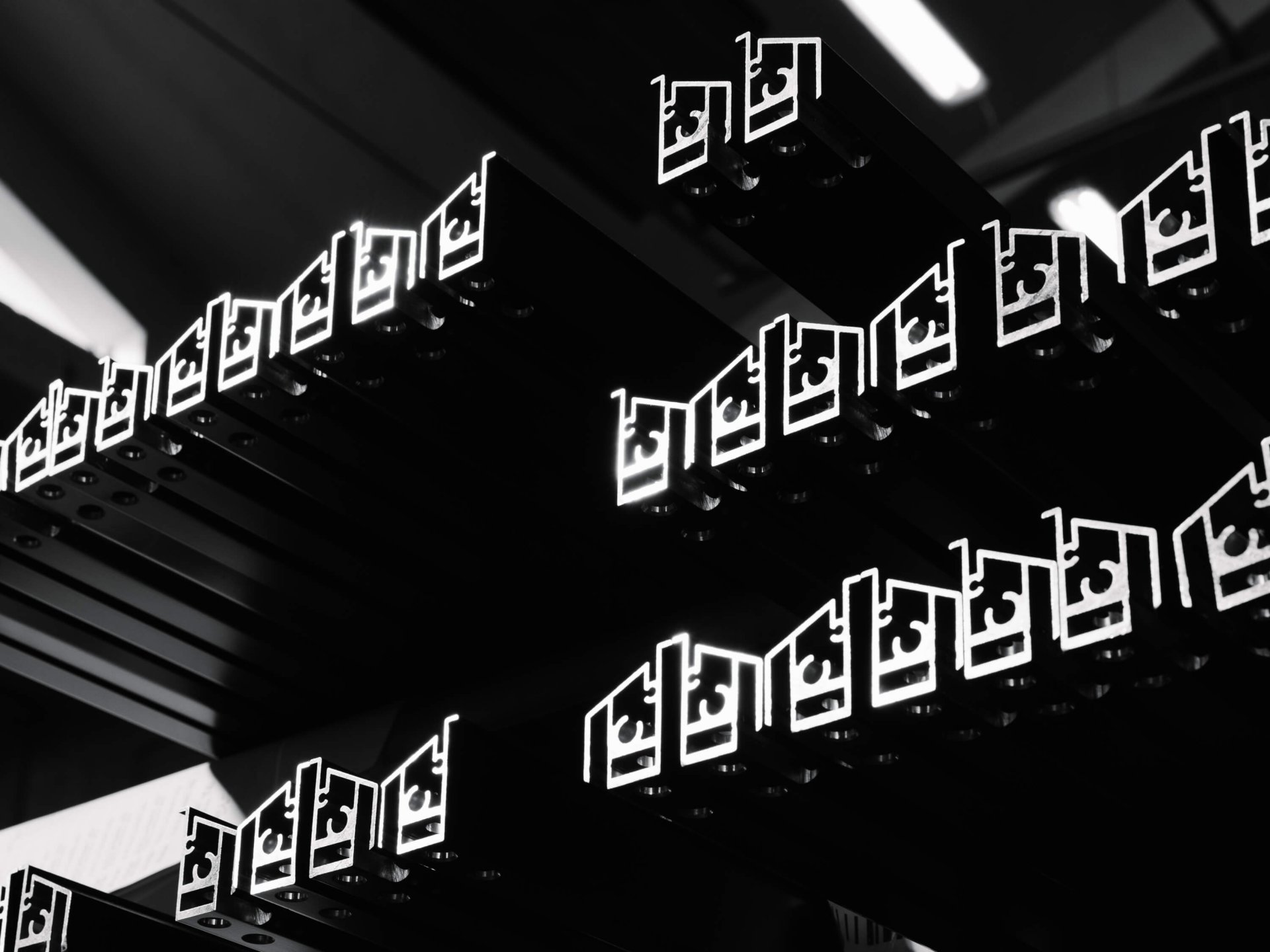
Extruded aluminum profiles
The chemical element represented by the symbol Al, by the number 13 in the periodic table, with an atomic weight of 26.98, is characterised not only by its surprising lightness, but also by its high electrical and heat conductivity capacity. Moreover, when exposed to an oxidising environment, an oxide film is formed on the surface which protects it from corrosion. It is malleable and ductile, making it easy to be processed, and moreover it is flexible, non-magnetic and non-flammable.
Aluminium alloys are to be found everywhere: in cans, in car wheel rims, in electrical wiring, in planes, in food wrapping, in medicine sachets, in toothpaste tubes. It is one of the most commonly used materials in the world, and the third most abundant in the earth’s crust, accounting for 8% of its composition, and yet it has an extremely recent history.
In nature it is not found in a pure state, it is to be found in a great number of minerals, and is, however, always combined with other elements from which it is not easy to separate. The first person who succeeded in doing so was the Danish scientist, Hans Christian Ørsted, who in 1825 succeeded in obtaining a few drops by means of reducing aluminium chloride AlCl₃ with a potassium and mercury amalgam.
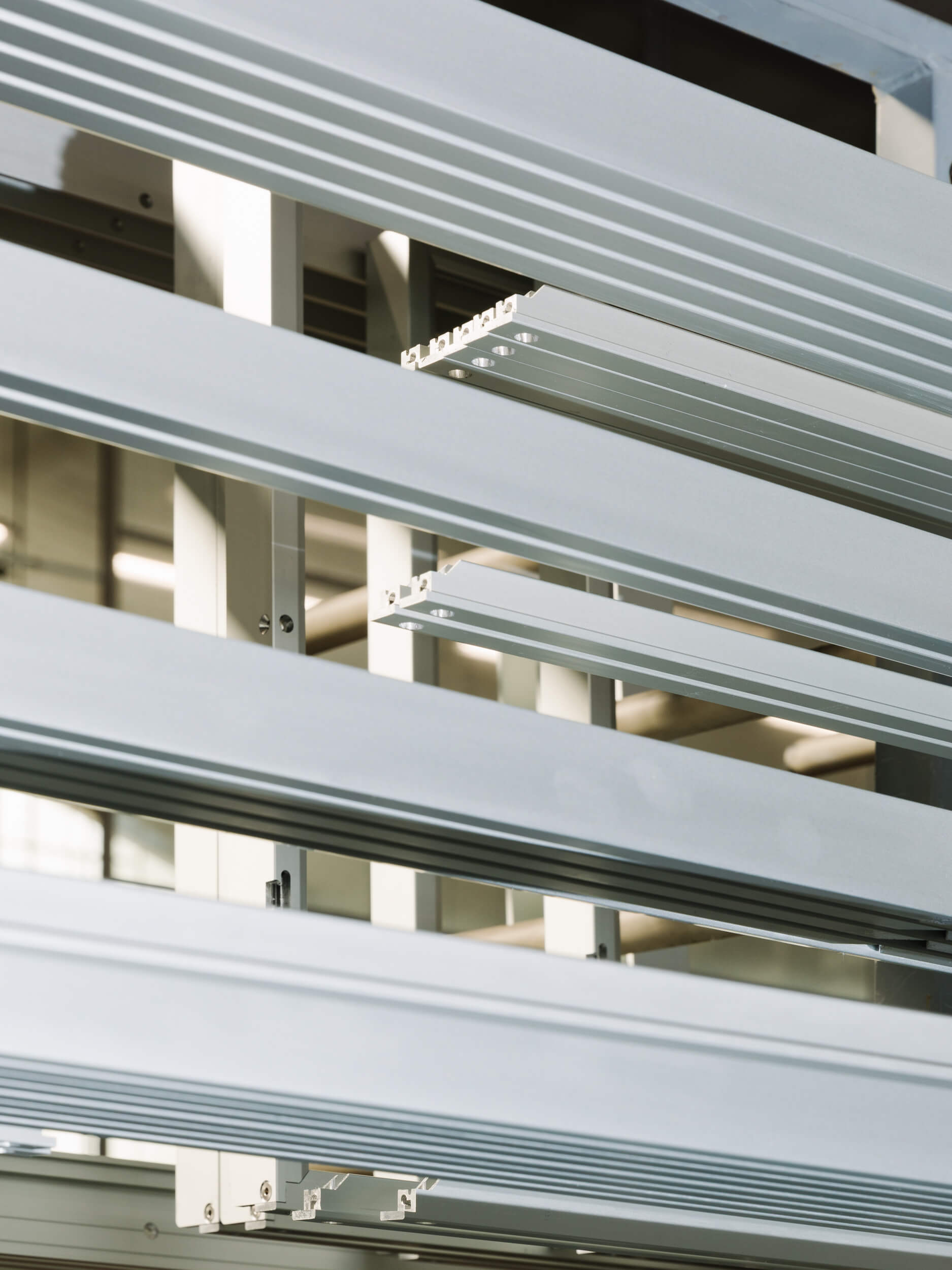
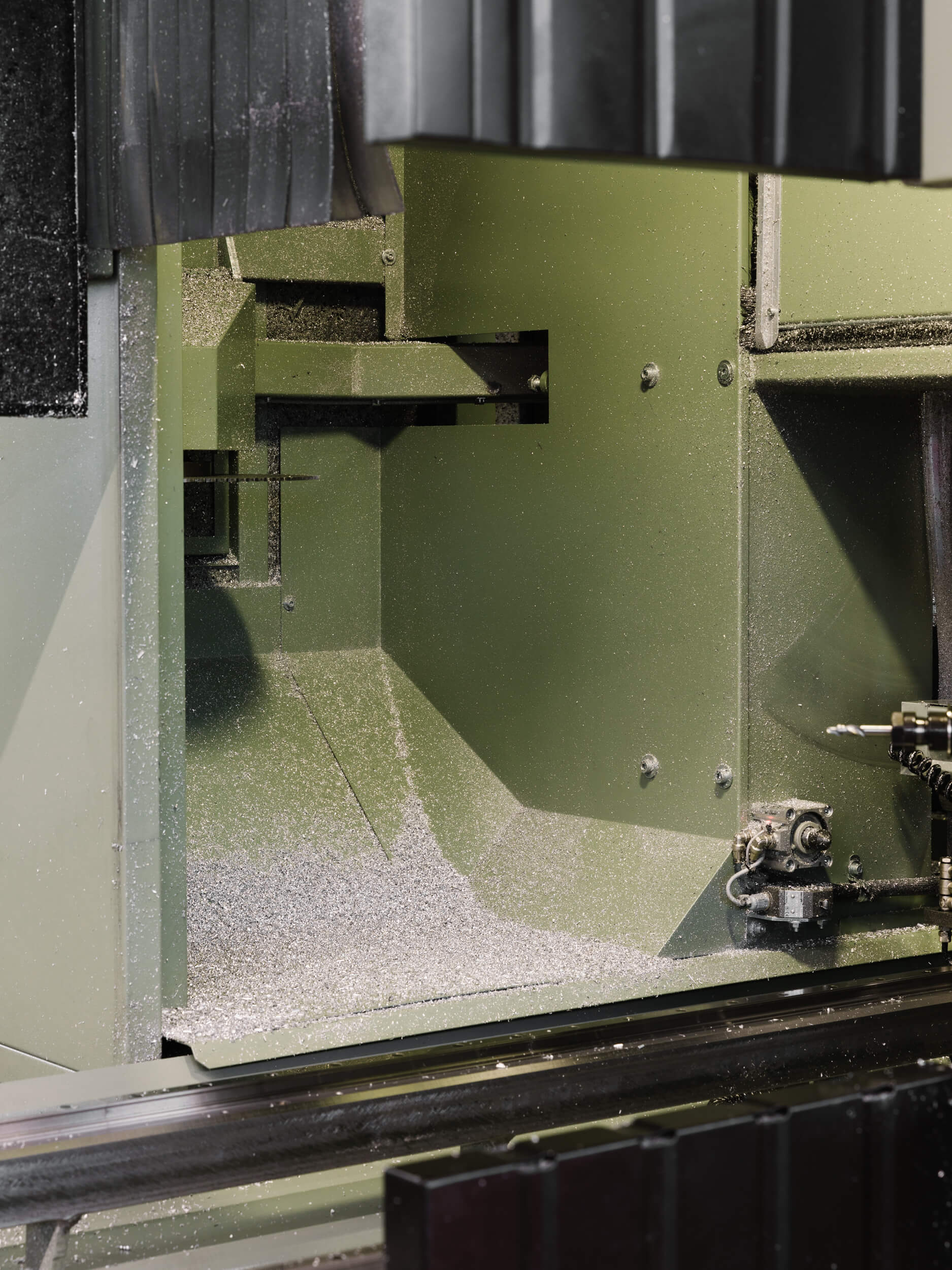
Legend has it that Napoleon III was an early patron of aluminium and amalgamated aluminium cutlery for his own bespoke use: guests had to make do with the golden set.
Things started to change in 1886, when the French scientist P.L. Héroult and his American colleague Ch.M. Hall patented a production method consisting in aluminium oxide electrolysis a few hours apart and independently from each other. Some years later in 1894, the Austrian chemist K. J. Bayer patented a chemical process of extracting alumina from Bauxite, the mineral discovered in 1821 by the geologist Pierre Berthier in the Provençal village Les Baux. The combination of these two processes, favored by the development of the production of electricity, shook the aluminium industry, leading to the inexorable rise of the metal which today is used versatilely everywhere. In the United States in 1884, 60 kilogrammes of aluminium were produced at the same price of silver. Today silver costs 260 times as much as aluminium and in 2017 alone 63.4 million kilogrammes were produced.
This incredible amount was obtained through the Hall-Héroult process, the Bayer process (88.6 million kilogrammes of alumina in 2017) and with bauxite mines (215 million kilogrammes in 2017). This mind-blowing success story does however have a dark side: its environmental impact. 4 tonnes of bauxite, 0.5 tonne of electrodes and 14,000 kWh of energy are needed to produce 1 tonne of primary aluminium. The extraction of one kilogramme of aluminia from bauxite can generate up to 2 kilogrammes of waste.
Throughout the world, at least 90 million tonnes are produced every year. This industrial waste has a specific name: Red mud (or bauxite tailings). It is a highly alkaline waste residue and cannot be disposed of easily as it is a risk for the eco system, thus making its laborious processing and storage processes also highly disputable. A number of processes have been developed to re-use these residues but they have proved to be unsustainable from an economic point of view and in addition simply generate further waste. In terms of energy the impact is just as startling: to produce a 33 cL can (16 grammes) more than 1000kj of energy is consumed, which is the same amount needed to keep a 10w bulb lit for approximately 30 hours.
Fortunately aluminium, unlike plastic, can be recycled ad infinitum and is 100% recyclable. Moreover, approximately 75% of the aluminium produced from 1988 to today (approximately one billion tonnes) is still in use. This means that the primary production of aluminium (consisting in extracting minerals from the earth’s crust, processing them with 21st century patented processes and returning the residues to nature) can be replaced by a circular process, meaning it develops off its own production without having the need to “extract ingredients” from the environment and without generating waste.
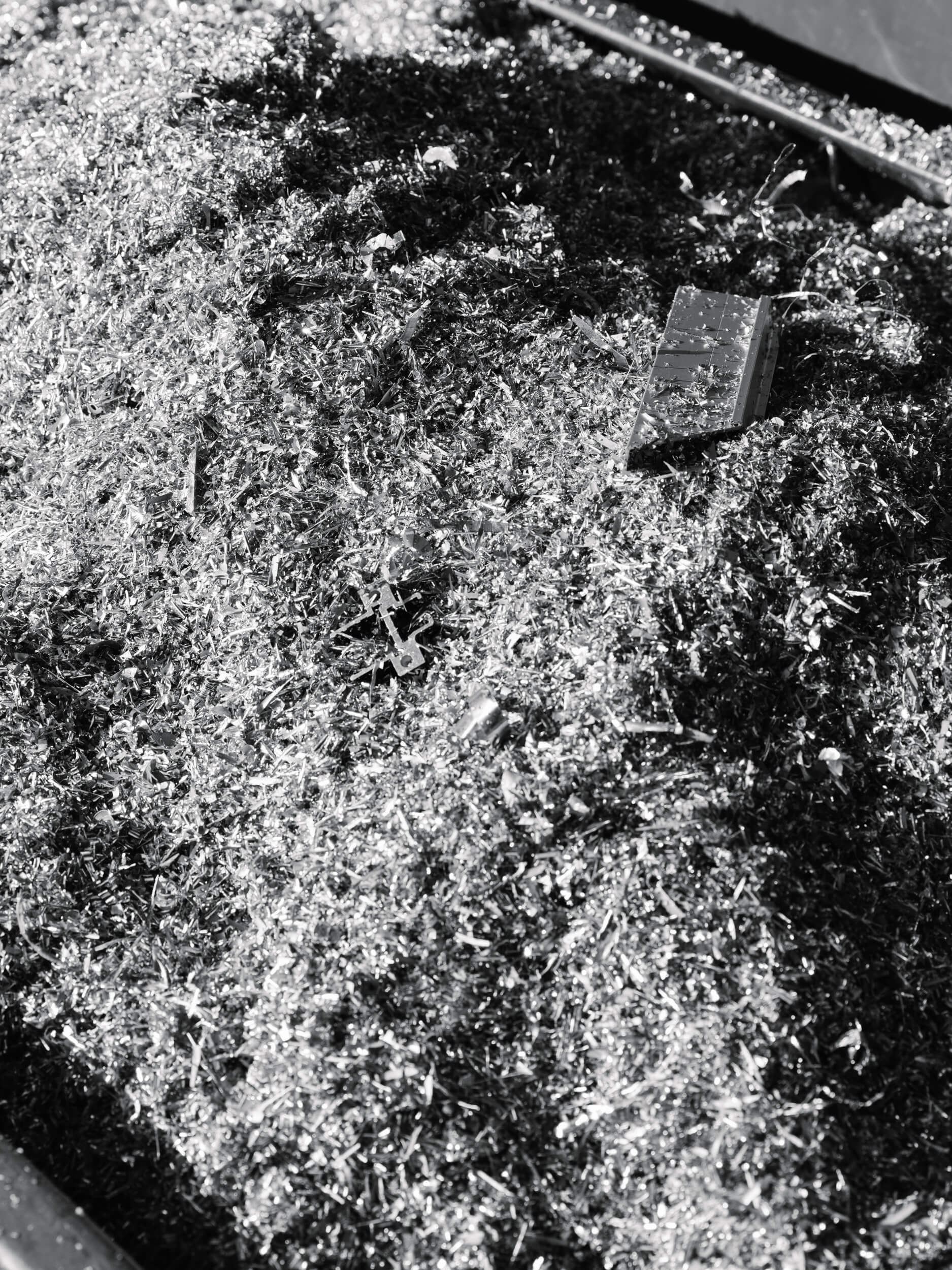
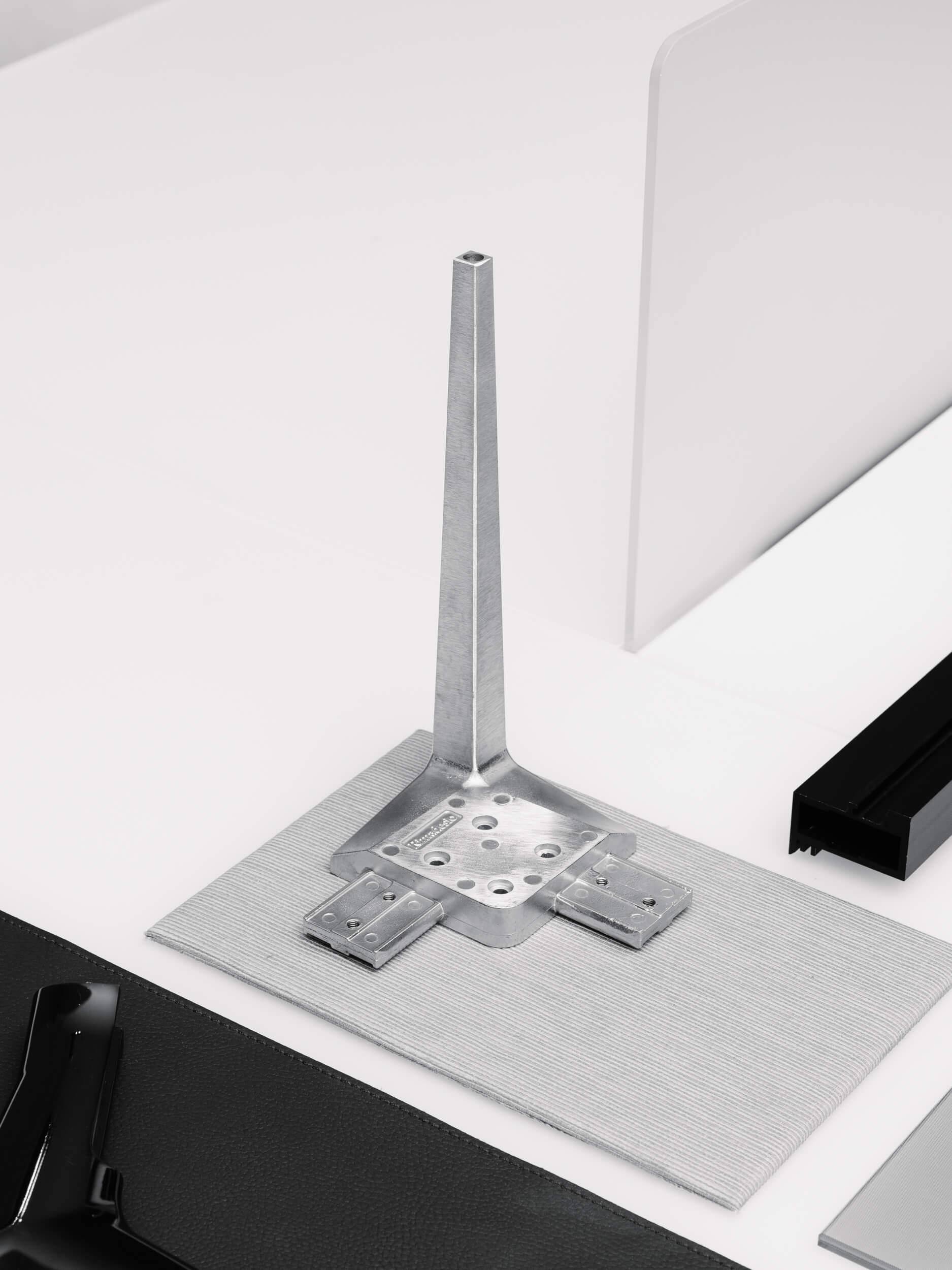
Today recycling aluminium is a reality: it covers 20% of global production and in Italy, the leading producer in Europe and the third largest one in the world, recycling means it is possible to recover 47,800 tonnes, that is to say, 70% of what is on the market. In terms of energy, the energy required for secondary production is 95% lower than that required for primary production. A can of recycled aluminium saves as much energy as you need to have the television on for three hours.
And recycling it in turn leads to saving even more energy:you need 3 cans to create glass frames, 37 for a coffee machine, 130 for a push-scooter, 800 for a bicycle. A virtuous cycle, which can be repeated ad infinitium. From its beginnings as a hazard for the environment, the production of aluminium has become an example of the circular economy par excellence: a system in which right from the outset non-organic materials are designed to be re-used in subsequent production cycles, without coming into contact with the biosphere.