Aluminio: un material valioso
«Utilizar otro metal en lugar de hierro fundido».
«¿El cobre?» dijo Morgan «¡No, todavía es demasiado pesado!
Tengo algo mejor que ofreceros».
«¿Y qué es ?», preguntó el comandante.
«El aluminio», respondió Barbicane.
«¡El aluminio!», exclamaron los tres colaboradores del presidente.
Julio Verne eligió el aluminio para construir la nave espacial que llegaría a la luna. Ligereza y resistencia, estas fueron las cualidades que hicieron que la gente optara por el metal blanco plateado en 1865, en “De la Tierra a la Luna”.
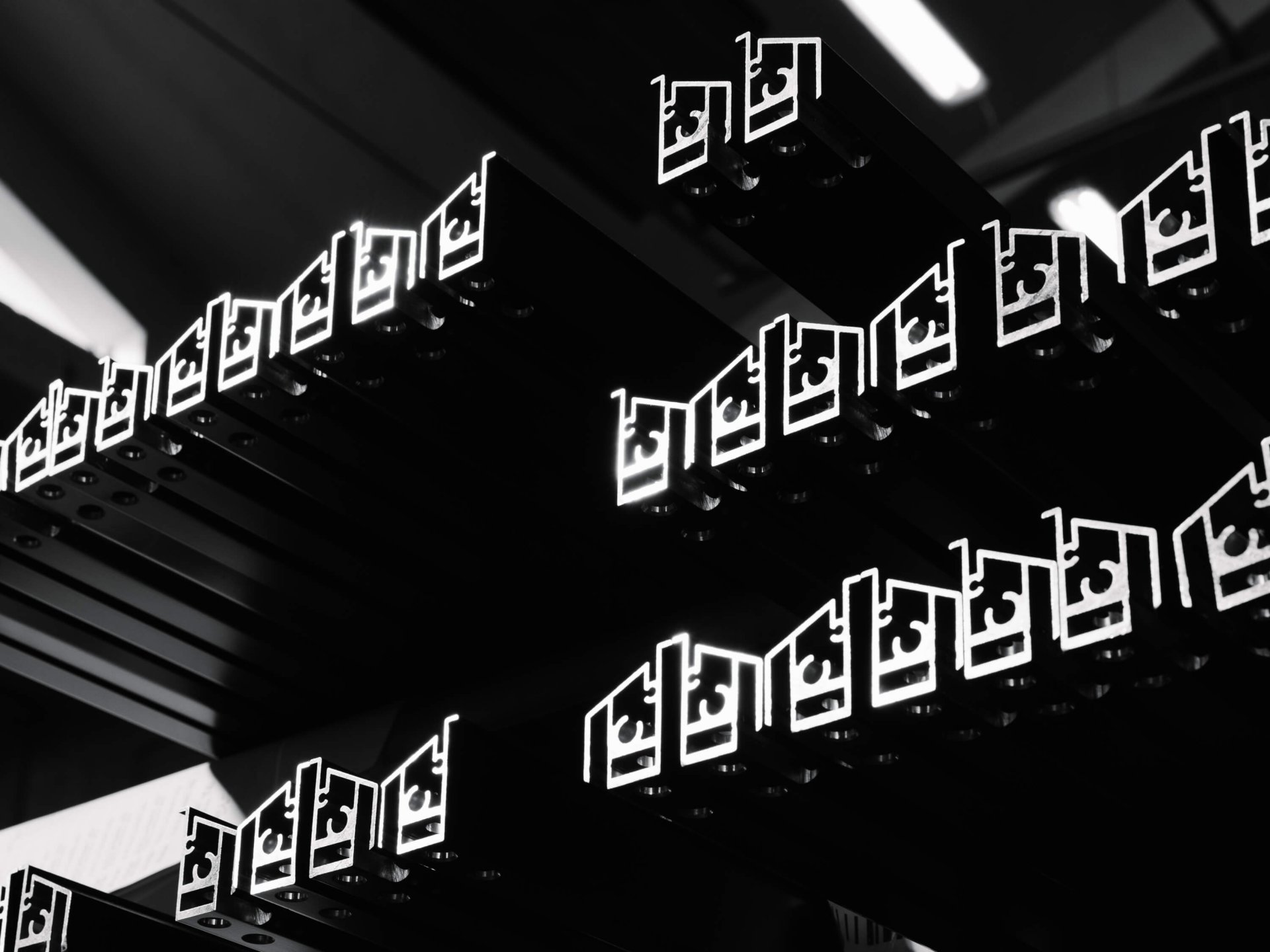
Extruded aluminum profiles
Elemento químico de símbolo Al, peso atómico 26,98 y número 13 en la tabla periódica, se caracteriza no sólo por su sorprendente ligereza, sino también por su elevada conductividad eléctrica y apreciable conductividad térmica. Además, cuando se expone a un entorno oxidante, se forma una película de óxido en la superficie que lo protege de la corrosión. Es maleable y dúctil, lo que facilita su mecanización, y es flexible, no magnético y no inflamable.
Las aleaciones de aluminio están por todas partes: en latas, llantas de coches, cables eléctricos, aviones, envoltorios de alimentos, en envases de medicamentos, tubos de pasta de dientes.
È uno de los materiales más utilizados en el mundo, y el tercer elemento más común en la corteza terrestre, que constituye alrededor del 8% y, sin embargo, la historia del aluminio es muy reciente.
En la naturaleza, no se encuentra en estado puro; está presente en muchos minerales, pero siempre combinado con otros elementos, de los que no es fácil separarlo. El primero fue el físico danés Hans Christian Ørsted, que en 1825 logró fabricar unas gotas reduciendo el cloruro de aluminio AlCl₃ con una amalgama de potasio y mercurio.
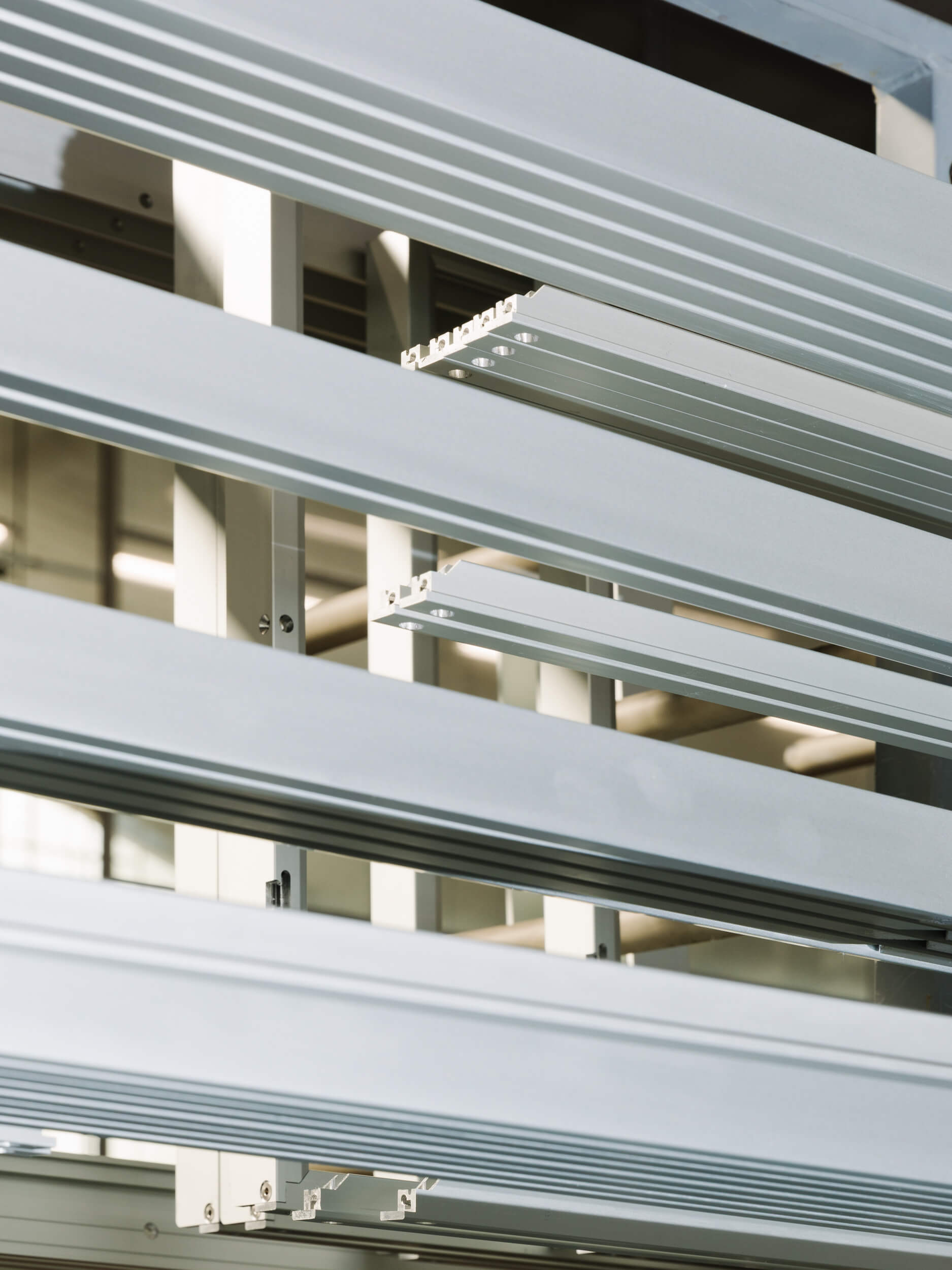
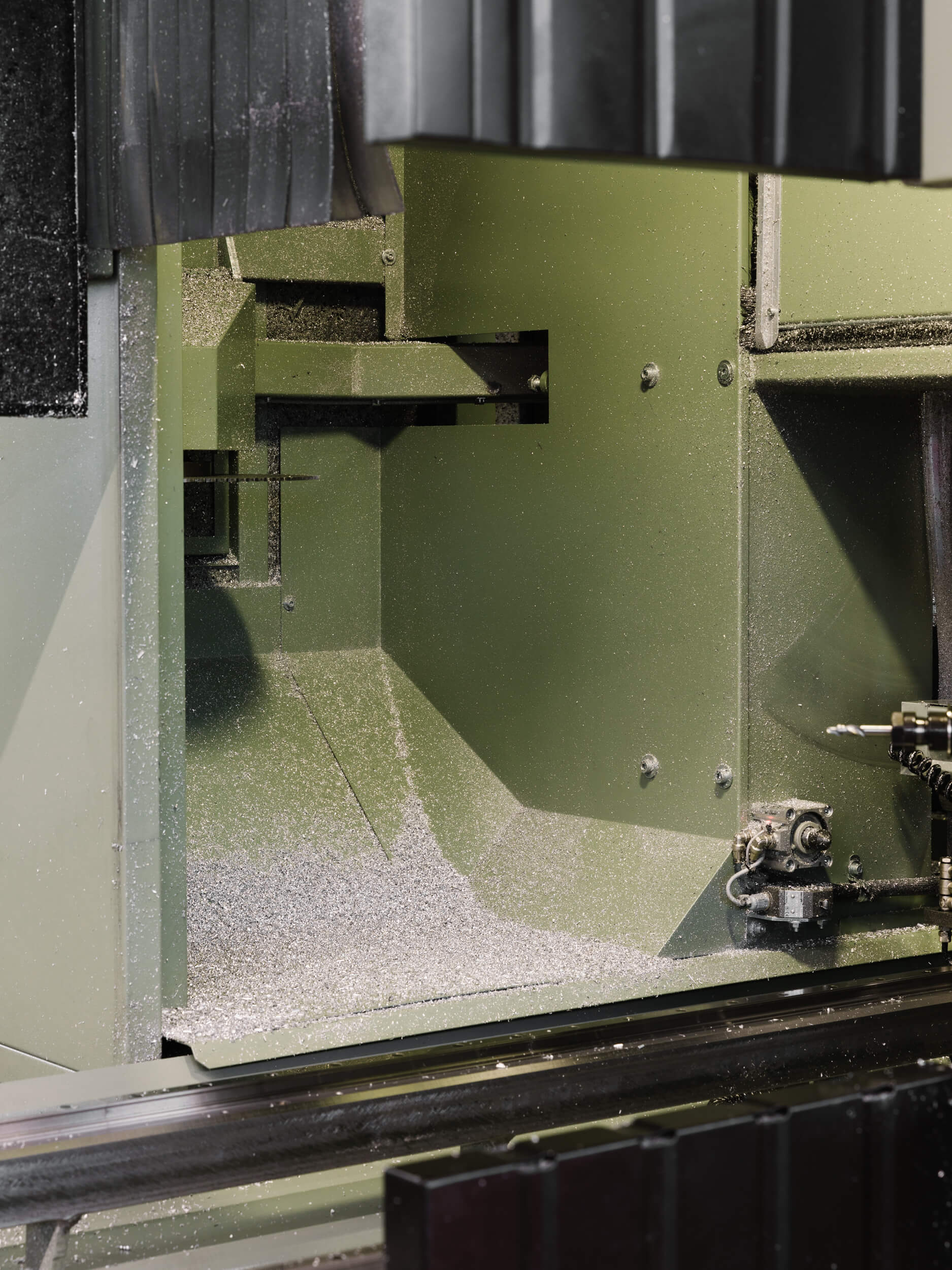
Cuenta la leyenda que Napoleón III mandó fundir cubiertos de aluminio para su uso personal y exclusivo: los invitados tenían que conformarse con el servicio de oro.
Las cosas empezaron a cambiar en 1886, cuando el científico francés P.L. Héroult y su colega estadounidense Ch.M. Hall patentaron un método de producción consistente en la electrólisis del óxido de aluminio (o alúmina) con horas de diferencia y de forma independiente. Unos años más tarde, en 1894, el austriaco K. J. Bayer patentó un proceso químico para extraer la alúmina de la bauxita, un mineral descubierto en 1821 por el geólogo Pierre Berthier cerca del pueblo provenzal de Les Baux. La combinación de estos dos procesos, apoyada por el desarrollo de la producción de electricidad, dio un vuelco a la industria del aluminio, permitiendo el ascenso imparable de este metal que ahora se utiliza en todas partes y para todo. En 1884 se produjeron 60 kilogramos de aluminio en Estados Unidos, al mismo precio que la plata. Hoy en día, la plata cuesta 260 veces más que el aluminio del que, solo en 2017, se produjeron 63,4 millones de kilogramos. Esta asombrosa cantidad se consiguió mediante el proceso Hall-Héroult, con el proceso Bayer (88,6 millones de kilos de alúmina en 2017) y la extracción de bauxita (215 millones de kilos en 2017).
La historia de este asombroso éxito tiene un lado oscuro: el impacto medioambiental. Para producir una tonelada de aluminio primario se necesitan 4 toneladas de bauxita, 0,5t de electrodos y 14.000kWh de energía. La extracción de un kilo de alúmina de la bauxita puede generar hasta dos kilos de residuos.
Cada año se producen al menos 90 millones de toneladas en todo el mundo. Estos residuos industriales tienen un nombre específico: lodos rojos. Debido a su altísima alcalinidad, no pueden eliminarse fácilmente y representan un importante factor de riesgo para el ecosistema, por lo que incluso los laboriosos procesos de tratamiento y almacenamiento a los que se someten son controvertidos. Se han desarrollado procesos para su reutilización, pero no son económicamente viables y generan residuos adicionales. En términos de energía, el impacto es igualmente impresionante: para producir una lata de 33 cL (16 gramos) se necesitan más de 1.000 kJ de energía, el equivalente a mantener una bombilla de 10 W encendida durante unas treinta horas.
Por suerte, el aluminio, a diferencia del plástico, puede reciclarse indefinidamente y es 100% reciclable. Además, aproximadamente el 75% del aluminio producido desde 1988 (unos 1.000 millones de toneladas) sigue en uso. Esto significa que la producción primaria de aluminio, que consiste en extraer minerales de la corteza terrestre, procesarlos con procesos patentados en el siglo XIX y devolver los residuos a la naturaleza, puede ser sustituida por un proceso circular, que se alimenta de su propio producto, sin necesidad de “sustraer” ingredientes del medio ambiente y sin generar residuos.
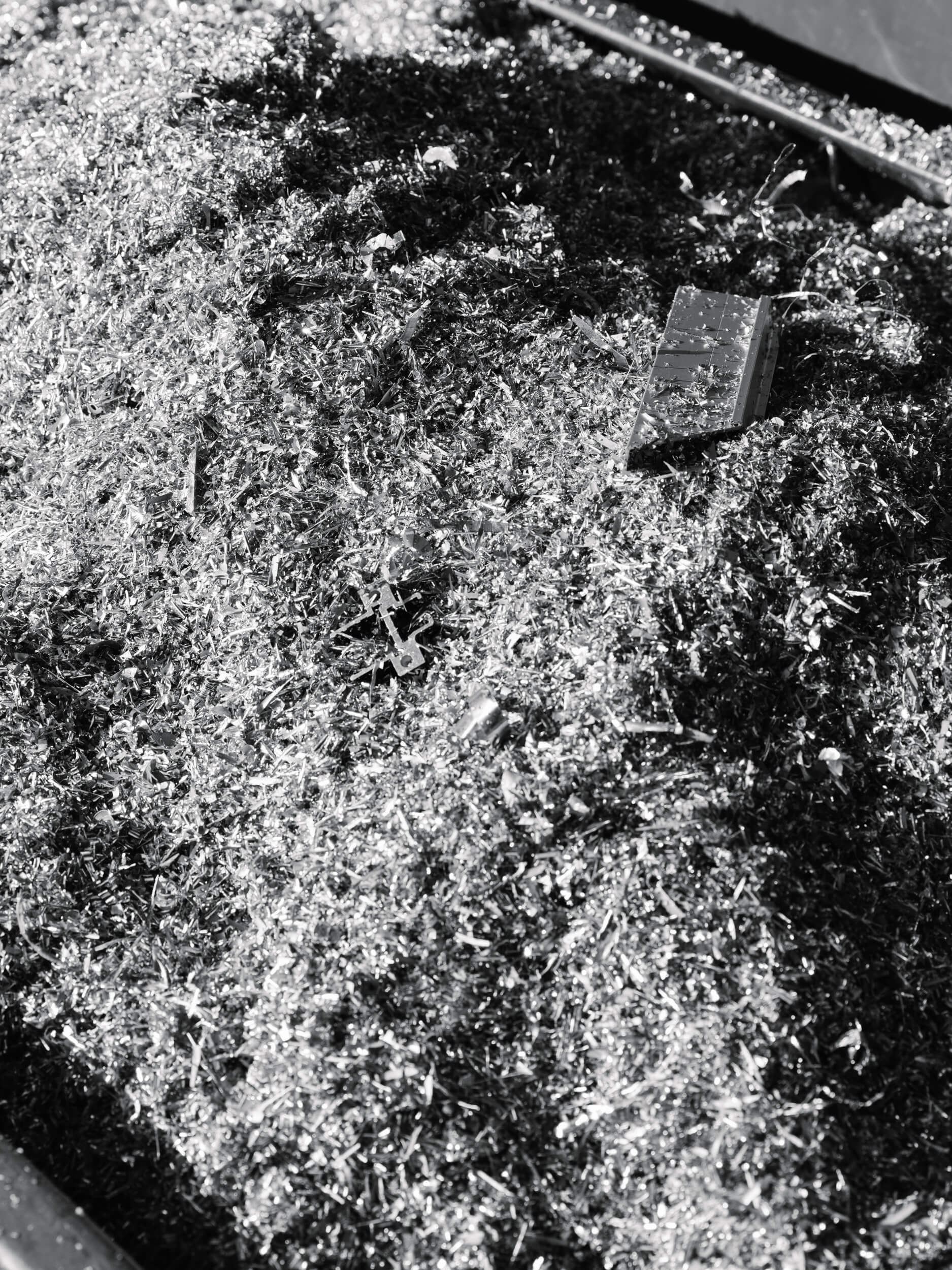
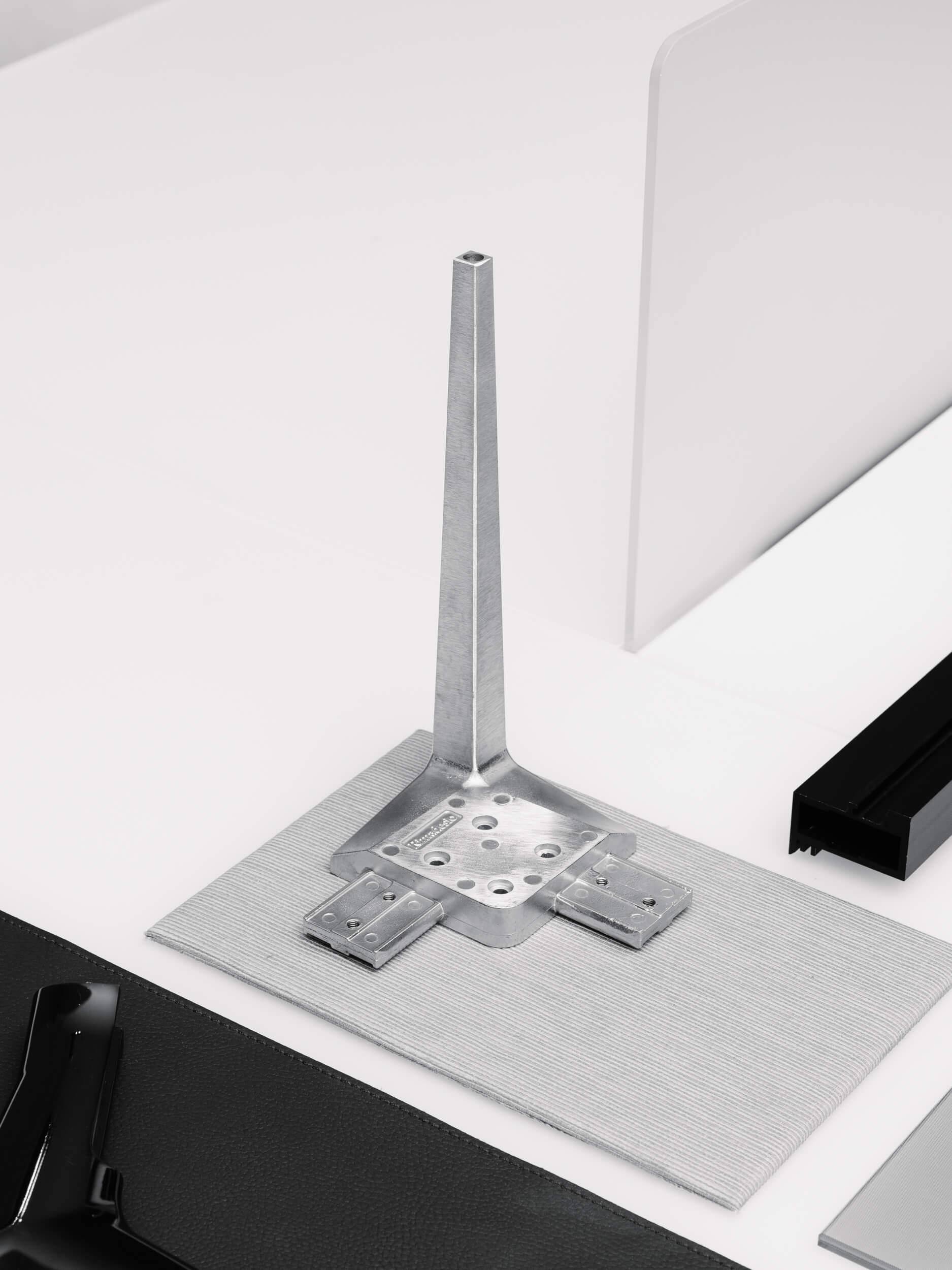
Actualmente el reciclaje del aluminio es una realidad: cubre el 20% de la producción mundial y en Italia, primer productor de Europa y tercero del mundo, permite recuperar 47.800 toneladas, es decir, el 70% del mercado. Desde el punto de vista energético, los recursos necesarios para la producción secundaria son un 95% menores que los necesarios para la producción primaria. Una lata de aluminio reciclada ahorra tanta energía como la que se necesita para mantener la televisión encendida durante tres horas.
Reciclarla, a su vez, permite ahorrar más energía: se necesitan 3 para fabricar una montura de gafas, 37 para una cafetera, 130 para un patinete y 800 para una bicicleta. Un ciclo virtuoso, que puede repetirse infinitamente. De ser un desastre medioambiental, la producción de aluminio se ha convertido en el ejemplo por excelencia de la economía circular: un sistema en el que los materiales no biológicos se diseñan desde el principio para ser reutilizados en los siguientes ciclos de producción, sin entrar en la biosfera.